At MSM Solar LLC, we believe in empowering homeowners with knowledge. Understanding the process behind solar panels can help you make informed decisions for your home. These systems convert sunlight into clean energy, using advanced technology to harness the power of the sun.
Our team has seen firsthand how Florida homeowners benefit from this knowledge, especially when choosing hurricane-resistant systems. With over 126 GW of solar capacity in the U.S., powering 23 million homes, it’s clear that this technology is here to stay.
We use Tier 1 panels with UL-listed components, specifically engineered to resist saltwater corrosion. Our NABCEP-certified team ensures installations can withstand 160 mph winds, a crucial feature for Panhandle weather patterns.
Discover how the 30% Federal Tax Credit combines with our $0 down financing to make this technology accessible. Plus, our 25-year warranty protects your investment through decades of tropical storms and sunshine.
Find Us Here:
Key Takeaways
- Solar panels convert sunlight into clean energy using advanced technology.
- MSM Solar LLC uses Tier 1 panels with UL-listed components for durability.
- Installations are designed to withstand 160 mph winds, ideal for Panhandle weather.
- The 30% Federal Tax Credit and $0 down financing make solar accessible.
- A 25-year warranty ensures long-term protection for your investment.
The Building Blocks of Solar Panels: Materials and Purpose
The foundation of any solar system lies in its carefully chosen materials. Each component is designed to maximize efficiency and withstand harsh conditions. From the core silicon to the protective layers, every piece plays a vital role.
Silicon: The Heart of Solar Cells
When I first held a silicon wafer, I marveled at its transformation from beach sand to a 99.999% pure semiconductor. This material is the backbone of cells, enabling them to convert sunlight into energy. By doping silicon with boron and phosphorus, we create an electrical field that powers your home.
Supporting Materials: Glass, Metal, and Plastics
Our panels use tempered glass thicker than standard models, crucial for hail protection in Florida storms. The aluminum frames aren’t just for structure; they undergo salt spray testing to prevent Gulf Coast corrosion. The plastic backsheet? We use triple-layered PET to block humidity that ruins cheaper panels.
- Silicon wafers form the core of solar cells, ensuring efficient energy conversion.
- Tempered glass makes up 76% of the panel’s weight, providing durability against extreme weather.
- Aluminum frames are tested for corrosion resistance, ideal for coastal environments.
- Triple-layered PET backsheets protect against humidity, extending the panel’s lifespan.
How Solar Panels Are Made: Step-by-Step Manufacturing
The journey of creating a solar panel is a fascinating blend of science and precision. Each step in the manufacturing process ensures the final product is efficient, durable, and ready to harness the sun’s power. Let’s dive into the key stages that transform raw materials into energy-producing marvels.
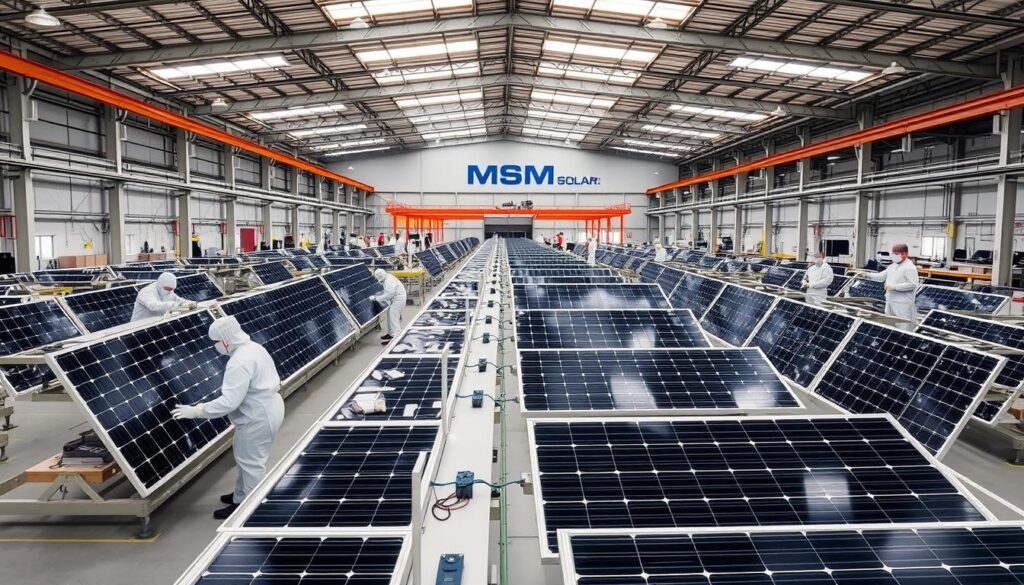
From Sand to Silicon: Purifying and Forming Wafers
I’ll never forget touring a factory where 2200°C furnaces transform sand into glittering silicon ingots. This high-temperature process creates metallurgical silicon, which is then purified to 99.999% purity. The result? Monocrystalline wafers with a single crystal structure, offering better efficiency in Florida’s partial shade conditions.
These wafers are then treated with boron and phosphorus to create an electrical field. This step is crucial for the cell’s ability to convert sunlight into energy. The precision here ensures every panel performs at its best.
Assembling the Solar Panel: Encapsulation and Framing
Encapsulation isn’t just glue; it’s a protective layer that ensures longevity. Our panels use EVA (ethylene-vinyl acetate) coating to prevent delamination from humidity swings. This is especially important in Florida’s humid climate.
The materials used in framing are equally critical. Aluminum frames undergo salt spray testing to resist corrosion, while tempered glass provides durability against extreme weather. Every component is chosen for its ability to withstand the elements.
Quality Testing: Ensuring Durability and Efficiency
Why do we test beyond UL standards? Because we want to ensure your panels last. Our thermal cycling chambers simulate 25 years of Florida seasons in just weeks. This rigorous testing guarantees the panels can handle everything from scorching summers to stormy winters.
Real-time monitoring is another layer of quality assurance. It allows us to track performance and address any issues immediately. That junction box? We seal it with military-grade epoxy so storm surges can’t compromise connections.
- Monocrystalline wafers ensure higher efficiency in partial shade.
- EVA coating prevents delamination from humidity.
- Thermal cycling tests simulate decades of weather in weeks.
- Military-grade epoxy seals protect against storm surges.
Types of Solar Panels and Their Manufacturing Differences
Choosing the right type of system for your home can feel overwhelming, but understanding the differences makes it easier. Each type has unique features, making it suitable for specific needs. Let’s explore the options to help you make an informed decision.
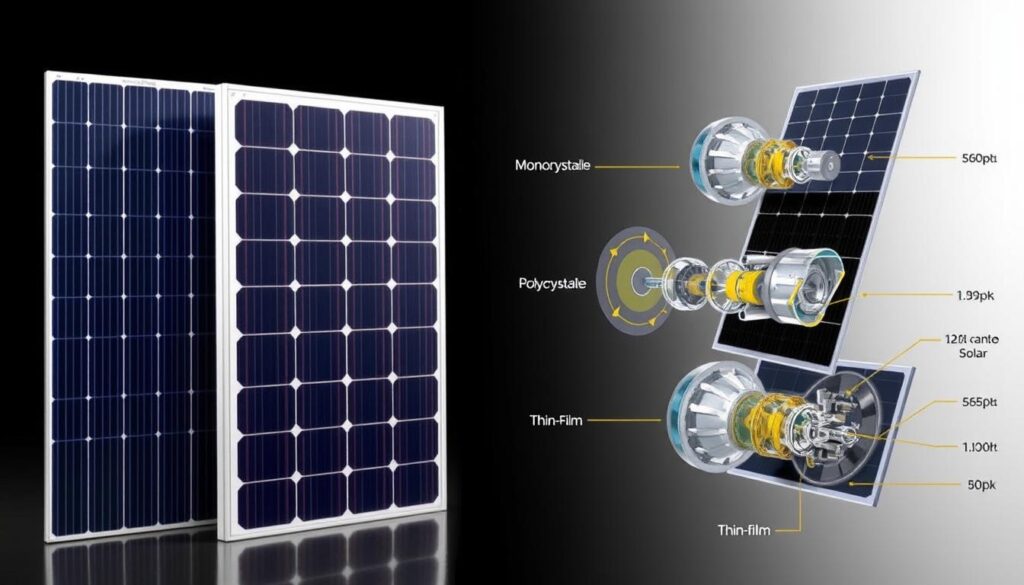
Monocrystalline vs. Polycrystalline: Efficiency and Cost
When my neighbor opted for polycrystalline, I explained how monocrystalline’s higher efficiency saves roof space. Monocrystalline systems use single-crystal cells, offering over 20% efficiency. This makes them ideal for homes with limited space.
Polycrystalline systems, on the other hand, are more affordable but slightly less efficient. They’re a great choice for larger areas where space isn’t a concern. However, in Florida’s partial shade conditions, monocrystalline’s performance often justifies the higher cost.
Thin-Film Panels: Flexibility and Niche Applications
Thin-film systems are perfect for unique applications, like historic Coral Gables homes with weight restrictions. These systems use lightweight materials, making them flexible and easy to install on unconventional surfaces.
However, thin-film systems typically have lower efficiency compared to crystalline cells. This means you’ll need more panels to generate the same amount of energy, which isn’t ideal for hurricane-prone areas. Additionally, some thin-film products use toxic materials like cadmium telluride, which we avoid in our manufacturing processes.
- Monocrystalline systems offer higher efficiency, saving roof space.
- Polycrystalline systems are more affordable but less efficient.
- Thin-film systems are flexible and lightweight, ideal for niche applications.
- Our premium cells maintain output even in partial shade.
- We avoid toxic materials in our manufacturing processes.
Conclusion: Trust MSM Solar LLC for Expert Solar Solutions
When it comes to reliable energy solutions, trust is everything. At MSM Solar LLC, we’ve installed over 7.2MW of solar panels across Florida, ensuring they withstand Category 4 winds and harsh weather. Our production guarantee isn’t just a promise—it’s insured through Lloyd’s of London.
As a family-owned business, we treat your home like our own. Our crew lives here, answers calls during hurricane warnings, and provides expert care. With a 25-year warranty and 5-star reviews, we’re proud to offer solar solutions that deliver peace of mind.
Ready to achieve energy independence? Join 1,300+ Florida families who’ve slashed their bills by 75%. Use our solar calculator for instant estimates and take the first step toward a brighter future.